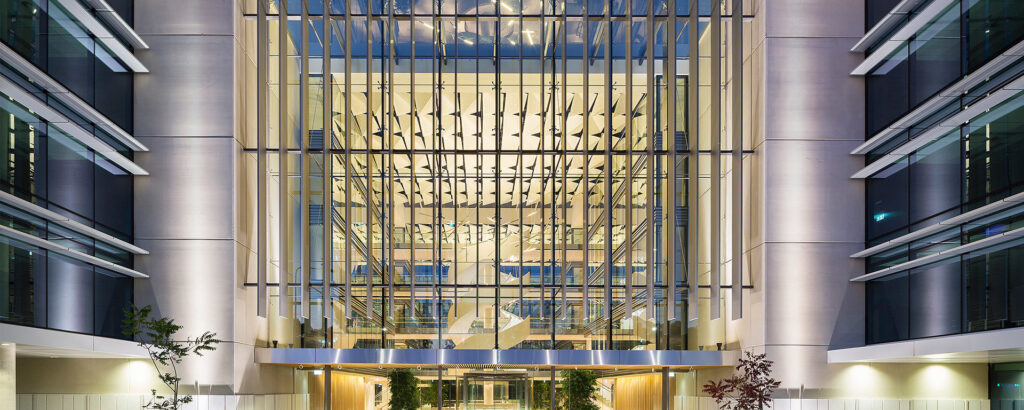
Project Details
Awarded the mechanical services D&C contract by Construction Control, Benmax recently completed work on the world class Canberra Grammar School (CGS) Music Centre and Auditorium project located at their Red Hill Campus in Canberra, ACT.
The independent school caters for students in pre-school to Year 12 and has a strong commitment to music through its longstanding CGS Music program. The new 3,100 sqm purpose-built facility is part of the school’s long term development plan and includes a 1,400-person acoustically tuned concert hall, 4 x music classrooms, 17 x tuition rooms, student commons, 450 sqm library and administration offices.
Construction of the facility required a specialist team involving leading consultants and expert trades. Benmax is proud to have been part of the hand selected team put together by Construction Control for the project, particularly given the innovative and unique mechanical services design features utilised on the build.
Subterranean design– sitting 12m below the neighbouring building, this structure is conditioned by an innovative modular polyvalent heat pump system coupled to a geothermal heat rejection loop. The team installed over 20km of geothermal pipework to support the system eliminating the need for mechanical equipment at ground level maintaining the panoramic and historic views of the school.
Acoustic considerations – due to the high acoustic sensitivity of the auditorium and associated practice rooms, significant attention was paid to the acoustic isolation and attenuation of the HVAC systems. More than 30 attenuators, the largest measuring 2.3m x 1.3m x 3m in size, are installed within the depths of the building ensuring the crisp notes of the performance are not distracted by the hum of the air conditioning equipment.
Modular construction – due to the basement location of the central chilled and heating water plant, as well as the primary air handling equipment for the auditorium, a modular approach was taken for the mechanical plant. Implementing an efficient modular plant room design eliminated costly support structures, reduced the plant size, decreased earthworks/dig size, and will allow for equipment maintenance and replacement even though the basement plant room is fully enclosed. All primary equipment components (i.e., heat pump units, fan motors) have been sized so that they can be removed via the main lift (from the basement to the ground level) over the lifecycle of the building.
Prefabrication and preassembled equipment – Benmax officially commenced on-site works in early 2021, however planning and design stages for the project were underway prior to that time to support the large-scale use of prefabricated and preassembled equipment during the build. This innovative construction method, made possible through the use of Building Information Modelling (BIM) technology, was utilised to support the tight delivery time frame required on the project, as well as ensuring the highest standards of quality control and on-site safety.
In this instance, 90% of the equipment for the primary plant room was prefabricated off-site in a controlled workshop environment. Using a variety of modules and skids and complete with all piping, duct, electrical, BMS, lagging and metal sheathing, the precision-made units were then transported to site with the Benmax team able to install the entire plant room in just one-day (8 hours). This process saved an estimated 5,000-man hours on site.
The Benmax team completed work on the project in mid-2022 with the facility now open and receiving outstanding feedback from students and patrons.
Awards
2024 ARBS Awards
2023 AIRAH Awards
2023 Master Builders ACT Building Excellence Awards
HVAC design specialists since 1986. Best practice is our standard.
We design, build and maintain specialised mechanical systems for commercial and industrial facilities to provide healthy, safe and efficient indoor environments for people to live, work and play. We’ve spent three decades building our reputation. We’ve done that by doing a good job, and getting another job.
Your local HVAC specialists
© Copyright 2023 Benmax Pty Ltd | Website developed by The Marketing GP
Legalities
Benmax acknowledges and pays respect to the past, present and future Traditional Custodians and Elders of this nation and the continuation of cultural, spiritual and educational practices of Aboriginal and Torres Strait Islander peoples.
We wish to acknowledge the Ngambri people, traditional custodians of the beautiful land on which our Headquarters resides.